1,涂層脫殼、剝離
①表面粗糙程度不夠或有灰塵吸附,使噴涂層附著力減小;應加強工件表面粗化及噴前清理工作。
②工件含有油脂,噴涂時油脂溢出,如球墨鑄鐵的曲軸等;噴前嚴格清除油污,并進行適當烘烤。
③壓縮空氣中有可見的油和水;盡量減少壓縮空氣中的油與水,必要時維修或更換壓縮空氣裝置。
④噴槍離工件太遠,金屬微粒未與工件充嵌合;應縮短噴槍與工件的距離。
⑤車削與拉毛、拉毛與噴涂各道工序相隔時問太長,待噴涂工件表面有氧化現象;應縮短表面預加、表面粗化、噴深等工序間隔時間。
⑥噴涂層在磨削機加工時,采用了氧化鋁砂輪,因而使涂層局部過熱而氧化;應正確選用砂輪做好冷卻措施。
⑦噴槍火焰不集中或偏斜,造成金屬微粒不能有力地粘著在工件表面;應撿修噴槍或更換之。
⑧工件的線速度和噴槍移動速度太慢,在噴涂過程中的夾雜物飄浮于工件表面,降低了附著強度;應調整工件的線速度,控制噴涂間間飄浮物。
2,涂層分層
①采用間隙噴涂,在將達到標準尺寸時沒有一次噴完,停噴時間太長;注意在間隙噴涂時,每次停噴時間要短。
②噴涂時壓縮空氣中的油和水濺在工件表面上;檢查空壓泵及附件氣路工作是否正常,常放水,特別是油水分離器應工作正常。
③每一層噴涂后有大量的灰塵吸附在工件表面上,使層與層之間有隔離或部分隔離現象;噴涂時應注意保持清潔,并作必要的防塵措施。
3,涂層碎裂
①噴涂時噴槍移動太慢,使一次噴涂的涂層太厚,并出現過熱現象;應保持正常的噴槍移動速度,一次不要噴得過厚。
②噴涂時噴槍離工件表面太近,使涂層過熱;應適當拉開噴槍與工件表面的距離。
③噴涂材料收縮率太大或含有較多的導致熱裂紋的元素(如S、P等);應選擇合適的噴涂材料,并注意盡量減少有害元素的含量。
④電弧噴涂時電流過大,火焰噴涂時使用氧化焰,使涂層厚氧化;應合理造擇噴涂參數和噴涂火焰。
⑤噴好后的涂層快速冷卻而導致碎裂;在噴厚的涂層時應注意冷卻速度。
⑥壓縮空氣中有油霧和水,降低了深層的結合強度;應及時解決壓縮空氣中的油和水。
⑦工件回轉中心不準,噴涂層有厚有薄,冷卻時收縮不均;應維修調正工件回轉中心的同心度。
4,涂層不耐磨
①噴槍離工件太遠,金屬微粒溫度低,與工件表面結合力小,其在工作時部分微粒脫落;應合理選擇噴涂距離。
②搭削時有大量砂粒嵌入涂層;應合理選擇磨削砂輪。
③金屬絲送進太快;應合理選擇送絲速度。
④金屬絲材料本身不耐磨;應選擇合格的噴涂材料。
⑤空氣壓力過低,噴槍離工件表面過遠,使結合強度降低;應合理選擇噴涂參數。
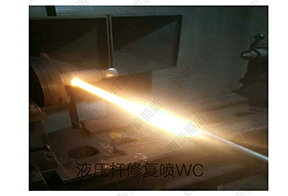